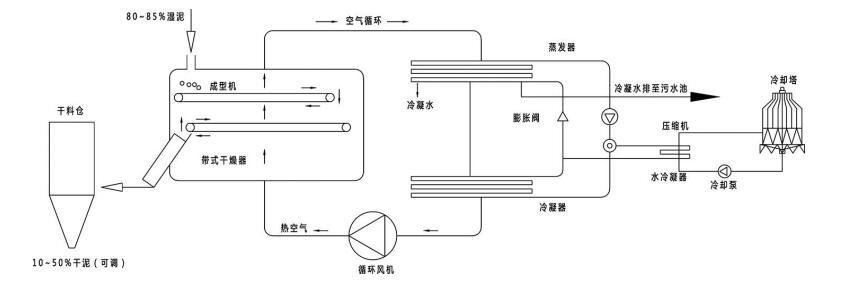
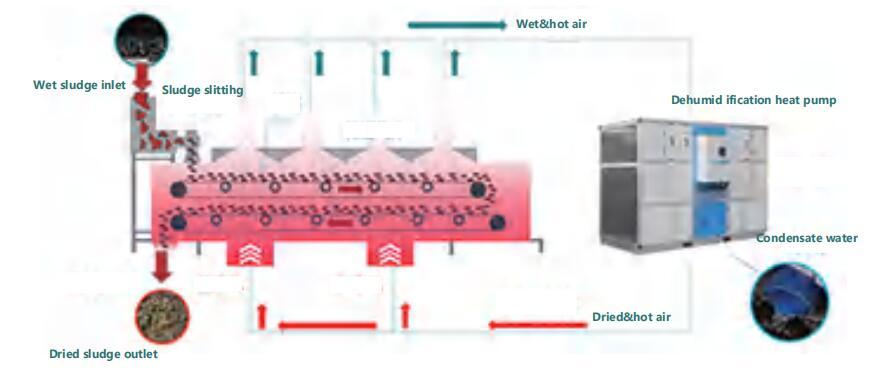
Model | QBGH-RB750FL | QBGH-RB1350FL | QBGH-RB3000FL | QBGH-RB6000FL | |||||
Rated standard water removal | kg/24h | 750 | 1350 | 3000 | 6000 | ||||
Rated standard water removal | kg/h | 31.3 | 56.3 | 125 | 250 | ||||
Rated standard operating power | Kw | 10 | 18 | 35 | 67 | ||||
Distribution power | Kw | 14 | 21 | 42 | 90 | ||||
Number of modules (sets) | 1 | 1 | 1 | 2 | |||||
Refrigeration System (Sets) | 1 | 1 | 4 | 8 | |||||
Dimensions | mm | 2625×1277×1850 | 3470×1277×2320 | 4100×2140×2240 | 6800×2140×2240 | ||||
Structural form | Ready | Ready | Ready | assemble | |||||
Unit weight | medical history | 1600 | 2000 | 3200 | 5800 | ||||
Cooling method | Air-cooled FL | ||||||||
Refrigerants | R134a | ||||||||
Drying temperature | 48~56(Return Air)/65~80(Supply Air) | ||||||||
Control system | Touch screen + PLC programmable controller | ||||||||
★ The amount of water discharged according to the rated standard varies depending on the mud properties, molding conditions, dust, etc., please consult an engineer for details. |
Model | QBGH-RB9000FL | QBGH-RB10800FL | QBGH-RB16200FL | |||||
Rated standard water removal | kg/24h | 9000 | 10800 | 16200 | ||||
Rated standard water removal | kg/h | 375 | 450 | 675 | ||||
Rated standard operating power | Kw | 99 | 118 | 174 | ||||
Distribution power | Kw | 119 | 142 | 209 | ||||
Number of modules (sets) | 3 | 4 | 6 | |||||
Refrigeration System (Sets) | 12 | 8 | 12 | |||||
Dimensions | mm | 9500×2140×2240 | 8050×3060×2750 | 11300×3060×2750 | ||||
Structural form | Ready | Ready | Ready | |||||
Unit weight | medical history | 8000 | 9100 | 12300 | ||||
Cooling method | Air-cooled FL | |||||||
Refrigerants | R134a | |||||||
Drying temperature | 48~56(Return Air)/65~80(Supply Air) | |||||||
Control system | Touch screen + PLC programmable controller |
Model | QBGH-RB21600FL | QBGH-RB27000FL | QBGH-RB32400FL | ||||
Rated standard water removal | kg/24h | 21600 | 27000 | 32400 | |||
Rated standard water removal | kg/h | 900 | 1125 | 1350 | |||
Rated standard operating power | Kw | 230 | 286 | 343 | |||
Distribution power | Kw | 276 | 343 | 412 | |||
Number of modules (sets) | 8 | 10 | 12 | ||||
Refrigeration System (Sets) | 16 | 20 | 24 | ||||
Dimensions | mm | 14550×3060×2750 | 17800×3060×2750 | 21050×306×2750 | |||
Structural form | assemble | assemble | assemble | ||||
Unit weight | medical history | 15500 | 17700 | 21900 | |||
Cooling method | Air-cooled FL | ||||||
Refrigerants | R134a | ||||||
Drying temperature | 48~56(Return Air)/65~80(Supply Air) | ||||||
Control system | Touch screen + PLC programmable controller | ||||||
★ The amount of water discharged according to the rated standard varies depending on the mud properties, molding conditions, dust, etc., please consult an engineer for details. |
Just say hello and we'll start a fruitful collaboration. Start your own success story.
Driven by environmental protection, the low-temperature belt sludge dryer uses energy circulation as its core logic and redefines the sludge drying treatment technology. This equipment converts the high energy consumption of traditional thermal drying into a sustainable energy closed loop through the coupling of thermodynamics and material science, providing an innovative path for sludge resource utilization that is both efficient and environmentally friendly.
Its technical core is to use the principle of low-temperature heat pump dehumidification and adopt convection hot air drying to dehydrate and reduce the wet material sludge on the mesh belt. In the fully enclosed drying room, the wet sludge carried by the multi-layer mesh belt flows in the opposite direction to the circulating hot air, and the water is migrated from the surface of the sludge by controlling the wind speed and temperature. As an energy hub, the heat pump system introduces the hot and humid air in the drying exhaust gas into the evaporator. When the temperature drops below the dew point, the water condenses and releases latent heat; the recovered heat is heated by the compressor and then re-injected into the drying chamber to form a lossless energy internal cycle.
The equipment structure design fully reflects the energy-saving concept. The mesh belt transmission system is driven by a variable frequency motor, and the running speed is adjusted in real time according to the moisture content of the sludge, ensuring the uniformity of drying while reducing ineffective energy consumption. The refrigeration system is used to cool and dehumidify the wet air from the drying chamber, and at the same time, the latent heat of water condensation is recovered and used to heat the dry air again.
Under the trend of intelligent evolution, this technological evolution not only broadens the application boundaries of the equipment, but also marks the upgrade of the sludge treatment industry from energy dependence to intelligent self-consistency.